Cold Rolled Steel vs. Hot Rolled Steel: Unveiling the Differences and Applications
- Share
- publisher
- Tianjin Yuantai Derun Steel Pipe Group
- Issue Time
- Mar 18,2024
Summary
Steel, the backbone of modern industry and construction, comes in various forms, each tailored for specific applications. Among the most common are cold rolled steel and hot rolled steel.
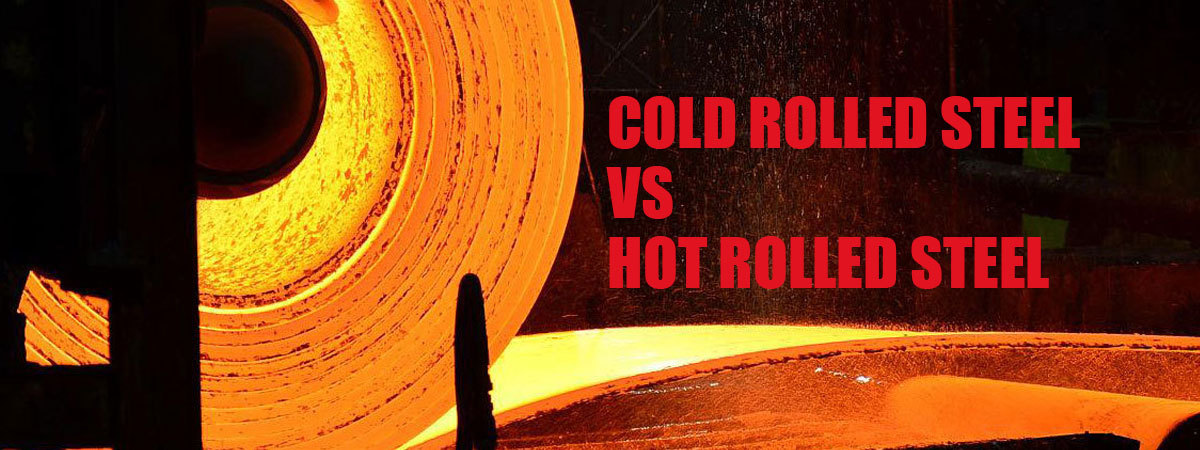
The rolling process relies on the friction created between the rotating rolls and the parts being rolled. This friction drags the parts into the gap between the rolls, compressing them and causing plastic deformation.
Rolled steel has 2 types,They are hot-rolled steel and cold-rolled steel respectively.It is important to understand the difference between hot-rolled steel and cold-rolled steel when selecting rolled steel for your project.
Process Differences:Hot Rolling Process VS Cold Rolling Process
The Hot Rolling Process
Hot rolled steel is steel that has been rolled at a temperature above its recrystallization temperature, typically 1700°F or higher. This process makes the material easier to form and work, making it easier to handle in subsequent operations.
The hot rolling process is a multi-stage metal processing technology, mainly involving the following steps:
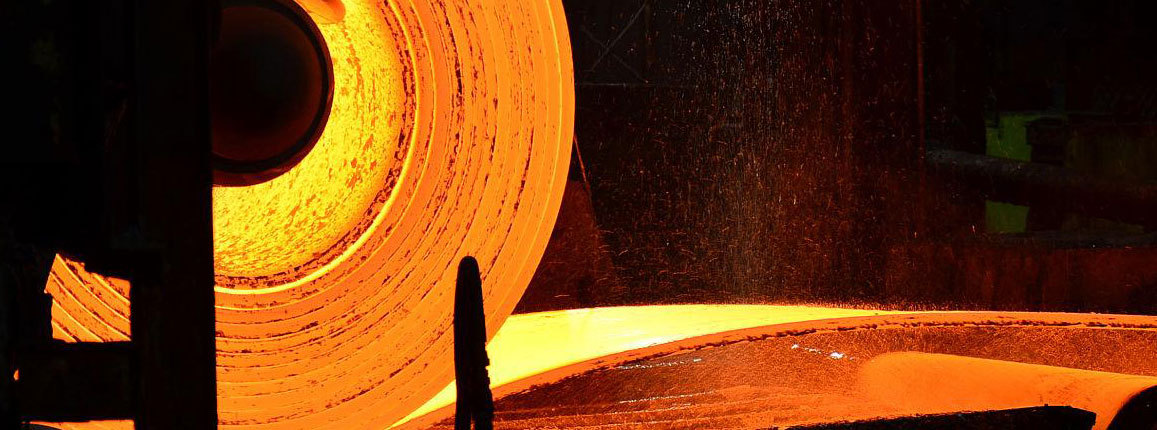
1. Preparation Of Raw Materials
The raw material for hot rolling is billet, which is first cut and pre-treated before hot rolling is carried out to make the shape and size of the billet more suitable for the rolling operation later.
2. Heating
Heating is a very critical step in the hot rolling process. By heating the metal billet to a high temperature, the plasticity and deformability can be improved to facilitate subsequent rolling operations. The heating method can be electric heating, flame heating or induction heating, etc., the specific choice according to the nature of the material and rolling requirements.
3. Roughing
Roughing is the first rolling step in the hot rolling process, the main purpose of which is to reduce the cross-section size and increase the length of the metal material.
4. Mid-rolling
Mid-rolling is an important step after roughing, where the metal is rolled further to achieve more precise dimensions.
5. Fine Rolling
Fine rolling is the last rolling step in the hot rolling process, mainly to further improve the dimensional accuracy and surface quality of metal materials.
6. Cooling
After fine rolling is completed, the metal material needs to be cooled to return it to its room temperature state.
7. Inspection And Finishing
After cooling, the metal material is inspected and sorted. The main purpose of inspection is to check the quality and dimensions of the metal material, including appearance, dimensional accuracy, chemical composition and mechanical properties. Finishing is mainly about cutting, shaping and sorting the metal material to make it into the final product that meets the customer's requirements.
8. Finished Product Packaging And Dispatch
The final step is to package and ship the metal product. Packaging of the finished product usually includes rust prevention, box material selection and marking to ensure that the product is not damaged during transport and storage. A final inspection of the finished product is also required to ensure that it meets the required quality standards.
The Cold Rolling Process
Cold rolling process refers to a series of processes, such as cold rolling at room temperature, using hot-rolled steel coils as raw materials, acid washing to remove oxide scales, and finally producing cold-rolled coils or sheets. The process flow of cold rolled steel is as follows:

1. Preparation Of Raw Material Hot-Rolled Coils
Hot-rolled steel coils, typically over 3 mm thick, are the main raw material for cold rolling. Prior to cold rolling, the raw materials must undergo pre-treatment work, including cleaning, polishing, and degreasing, to ensure stable material quality.
2. Preprocessing
During the cold rolling process, a protective film is applied to the steel surface to prevent oxidation, contamination, corrosion, and other damage.
3. Rolling Steel
The main process in cold rolling is rolling. Rolling is divided into two types: multi-pass roll rolling and single pass roll rolling. Multi-pass roll rolling can make the steel thickness, width and other attributes uniform and stable. Single pass roll rolling, on the other hand, adjusts the steel thickness by pressing it several times.
4. Annealing
After rolling, steel undergoes an annealing process. Annealing involves heating the steel to a specific temperature and then cooling it in a particular way to alter its properties. Usually, the steel is heated to a temperature slightly above room temperature and then cooled using nitrogen or hydrogen injection. This process enhances the steel's plasticity and toughness, thereby improving its mechanical properties.
5. Trimming
Trimming involves cutting the steel around the edges to remove defects such as curling and burring, and to flatten the steel. This can be done using a cutter or chemical process.
6. Packaging
After trimming, the steel must be packaged to maintain its quality and prevent contamination, corrosion, and other damage to its surface. Packaging methods include tying with steel tape, wrapping with plastic film or cardboard, and more.
In addition, surface treatments such as oiling, galvanising or spraying can be applied during the cold rolling process to enhance its durability and rust resistance, making it more suitable for use in external environments.
Key points of process differentiation:
1. Rolling is divided into cold rolling and hot rolling, with recrystallization temperature as the distinguishing point;
2. Cold rolling is generally used for producing strips, with a higher rolling speed, while hot rolling is generally used for producing plates and coils, with a slower rolling speed;
Distinguishing Characteristics:
1. Surface Finish:
- Hot rolled steel usually has a rough, scaly surface, oxidation, and low smoothness, which are caused by the high temperature during its production process.
- Cold rolled steel boasts a smooth, polished surface, thanks to the additional processing steps that refine its appearance.
2. Dimensional Tolerances:
- Hot rolled steel tends to have looser dimensional tolerances compared to cold rolled steel, making it suitable for applications where exact dimensions are less critical.
- Cold rolled steel offers tighter dimensional tolerances, making it preferred for applications requiring precise shapes and dimensions.
3. Mechanical Properties:
- Hot rolled steel has relatively low strength, but good plasticity and high ductility. Easy processing and good weldability, among other excellent properties
- Cold rolled steel has high strength and hardness, but slightly weaker plasticity. Cold rolled steel has a fine surface finish and controllable grain structure, making it an ideal choice for applications that require precision and durability.
4. Thickness:
- Hot rolled steel plates are divided into two types: thick plates (with a thickness greater than 4mm) and thin plates (with a thickness of 0.35-4mm);
- There is only one type of cold-rolled steel plate, which is thin plate (with a thickness of 0.2-4mm).
5. Cost:
- The surface flatness of hot-rolled steel is poor, and there are relatively few processing procedures, so the price of hot-rolled steel products is lower,
- The processing flow of cold rolled steel is diverse, with a flat and smooth surface, high hardness, toughness, and precise dimensions, making it more expensive.
6. Internal Stress:
In terms of internal stress, hot-rolled steel usually has relatively low internal stress due to the lack of additional process treatment. Cold rolled steel, due to these additional treatments, will generate internal stress within the material. If the steel is not stress relieved before cutting, grinding, or welding, cold-rolled steel may cause unpredictable deformation.
Application Differences:
1. Hot Rolled Steel:
- Structural components in construction, such as beams, columns, Steel Security Door, Fireproof Door and rails.
- Automotive frames, chassis, and structural components.
- Railroad tracks, shipbuilding, and heavy equipment manufacturing.
- Industrial machinery and agricultural equipment.
2. Cold Rolled Steel:
- Automotive body panels, doors, hoods, and fenders.
- Appliance components such as panels, cabinets, and housings.
- Furniture, shelving, and storage systems.
- Precision engineering components in aerospace, electronics, and telecommunications.
The Final Words
In conclusion, while both cold rolled steel and hot rolled steel originate from the same material, their processing methods result in distinct characteristics and suitability for different applications. Hot rolled steel, with its rough surface finish and looser dimensional tolerances, excels in structural and heavy-duty applications. Meanwhile, cold rolled steel, prized for its smooth surface finish and precise dimensions, finds favor in industries where accuracy and aesthetics are paramount. By understanding the differences between these two variants, manufacturers and engineers can make informed decisions to optimize performance and efficiency in their respective applications.