How To Understand Quenching, Tempering, Annealing, And Normalizing?
- Share
- publisher
- Wu Mingyue
- Issue Time
- Sep 10,2024
Summary
Understand Quenching, Tempering, Annealing, And Normalizing 4 hot treatment.
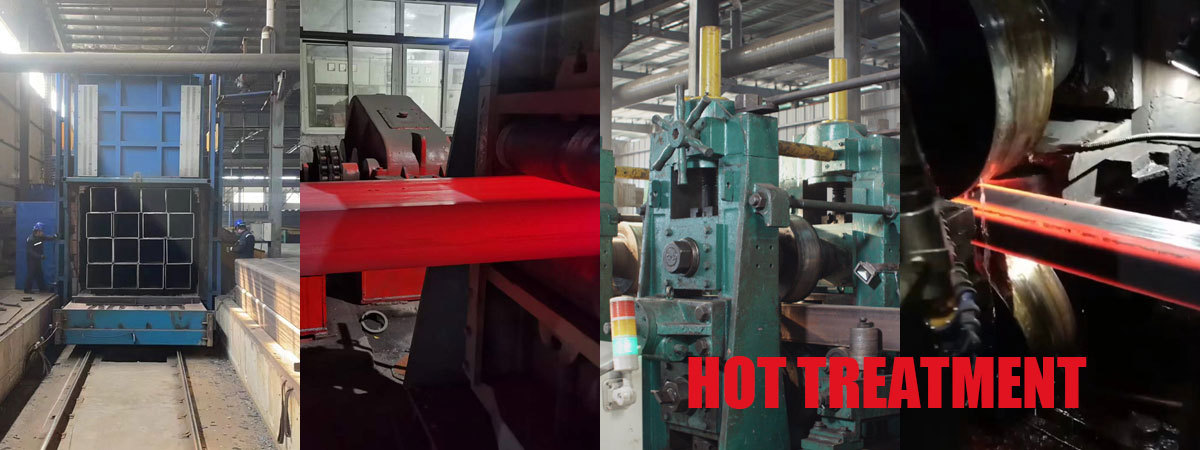
Quenching, Tempering, Annealing, And Normalizing is 4 common heat treatment in steel industry.However, there are still many people who do not fully understand the four heat treatment methods. This article will use concise language to explain them. I believe that after reading this article, you will have a general understanding.
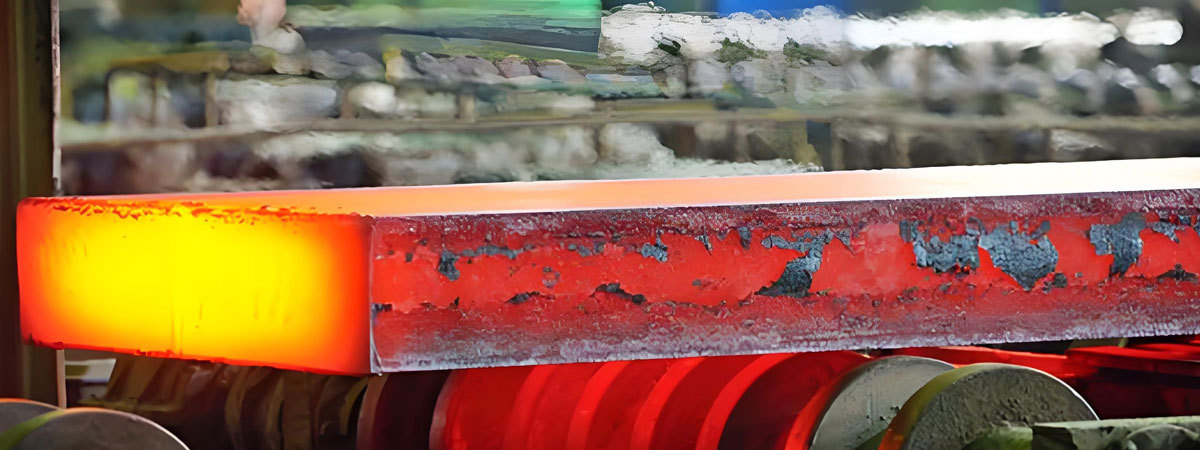
Do You Know Why Heat Treatment Is Necessary?
Heat treatment is to obtain some properties that the original steel product does not possess, such as:
1. Strength
2. Hardness
3. Resilience
4. Machinability
5. Corrosion resistance performance
6. Wear resistance performance
7. Impact resistance
8. Construction performance
What Materials Are Suitable For Heat Treatment?
Carbon Steels
|
Alloyed with carbon to improve hardness and strength.
|
Alloy Steels
|
Containing additional elements like chromium, nickel, or molybdenum for enhanced properties.
|
Stainless Steels
|
Certain grades can be heat treated to increase hardness.
|
Tool Steels
|
Designed for high wear resistance and toughness.
|
Cast Irons | Can be treated to improve hardness and wear resistance. |
Aluminum Alloys | Certain types can be heat treated to enhance strength and corrosion resistance. |
Titanium Alloys | Heat treatment improves mechanical properties. |
Copper Alloys | Some can be heat treated for improved strength. |
What Are The Common Types Of Heat Treatment Methods?
In daily industrial production, the common heat treatment methods mainly include Quenching, Tempering, Annealing, and Normalizing. Different heat treatment methods can result in different performance changes for steel components. Let's take a look at their characteristics and specific applications separately below.
Quenching
Quenching is one of the most common heat treatment methods. Usually, the workpiece needs to be heated to a certain high temperature, usually 800-900 degrees Celsius, and quickly placed in a coolant (water or oil) for the heat treatment process of rapid cooling of the workpiece. After rapid cooling, the workpiece can improve its hardness and wear resistance.
Name
|
Quenching Temperature
|
Cooling Medium
|
Cooling Rate
|
Quenching
|
800-900℃
|
Water,oil
|
Fast
|
Tempering
Tempering is the second heat treatment process, whose main purpose is to reduce or eliminate internal stress in quenched workpieces, reduce hardness and strength, and improve their ductility or toughness. Specifically, tempering is the process of reheating quenched workpieces to an appropriate temperature below the lower critical temperature, holding them for a period of time, and then cooling them in air or water. According to the different tempering temperatures, it can be divided into low-temperature tempering (150-250 ° C), medium temperature tempering (350-500 ° C), and high-temperature tempering (500-650 ° C). Sometimes tempering and quenching need to be used in combination.
Name
|
Tempering Temperature
|
Cooling Medium
|
Cooling Rate
|
Tempering
|
Below the lower critical temperature Ac1
|
Water,Air
|
Fast Or Slow Or According The Actual Situation
|
Tempering Classification
|
Temperature Range
|
Tempering Purpose
|
Low Temperature Tempering
|
150-250 ° C
|
The goal is to keep workpieces hard and resistant to wear during quenching. After tempering, you get tempered martensite, which is the microstructure from low-temperature tempering of quenched martensite. It's 58-64HRC, hard, and resistant to wear.
|
Medium Temperature Tempering
|
350-500 ° C
|
The goal is to achieve high elasticity, yield point, and toughness. After tempering, tempered martensite is obtained. This is a multiphase structure with small spherical carbides distributed within the ferrite matrix.
Mechanical Properties: 35-50HRC, high elasticity, yield point, and toughness. |
High Temperature Tempering
|
500-650 ° C
|
The goal is to get strong, flexible, and tough materials.
After tempering, the material becomes tempered martensite. This is a multiphase structure with carbides distributed in the ferrite matrix.
Mechanical properties: 25-35HRC, with good comprehensive mechanical properties. |
Annealing
Annealing is a heat treatment method that slowly heats the workpiece to an appropriate temperature (usually 780-900 degrees for carbon steel), holds it for a certain period of time, and then cools it down with the furnace cooling. After annealing, the hardness of the workpiece is lower, which removes internal stress and can also uniformly refine the internal structure of the material, preparing for the next step of heat treatment (quenching, etc.).
Type
|
Heating Speed |
Annealing Temperature
|
Holding Time |
Cooling Medium
|
Cooling Rate
|
Carbon Steel Annealing
|
Slowly |
780-900 ° C
|
1-2 Hour Or According The Actual Situation |
furnace cooling
|
Slowly
|
Stainless Steel Annealing
|
Slowly |
1040-1100° C
|
1 Hour |
furnace cooling
|
Slowly
|
The Purpose Of Annealing
Reduce hardness: Through annealing treatment, the hardness of metal materials will be reduced, making them easier to cut.
Relieve stress: Annealing can release residual stress generated in the material during processing, preventing deformation and cracking of the workpiece.
Enhance ductility and toughness: Annealing can improve the ductility and toughness of materials, making them less prone to fracture when subjected to external forces.
Changing microstructure: Annealing can alter the microstructure of materials, giving them better mechanical and physical properties.
Normalizing
Normalization is a heat treatment process that heats steel components to a temperature of 30-50 ℃ above Ac3, and then holds them for a period of time before being air cooled out of the furnace. The main characteristic of normalizing is that the cooling rate is faster than annealing, but slower than quenching, which can refine the crystalline grains of steel and improve strength and toughness in slightly faster cooling.
The main purpose of normalizing is to refine grain size, adjust hardness, eliminate carbide network, and prepare the structure for subsequent processing, spheroidization annealing, quenching, etc. Normalization can be used for various types of steel and castings, such as low carbon steel, medium carbon steel, tool steel, bearing steel, carburizing steel, etc. It can eliminate internal stress, refine structure, improve hardness, strength, and wear resistance.
Type
|
Normalizing Temperature
|
Cooling Medium
|
Cooling Rate
|
Normalizing
|
757-962° C
|
Air, Spray, Blow Cooling
|
Faster than annealing but lower than quenching
|
Normalizing Application
The main application scope of normalizing includes:
① Used for low carbon steel, after normalizing, the hardness is slightly higher than annealing, and the toughness is also good, which can be used as a pre-treatment for cutting processing.
② Used for medium carbon steel, it can replace quenching and tempering treatment (quenching+high-temperature tempering) as the final heat treatment, and can also be used as a preparatory treatment before surface quenching by induction heating method.
③ Used for tool steel, bearing steel, carburizing steel, etc., it can reduce or inhibit the formation of network carbides, thereby obtaining a good microstructure required for spheroidization annealing.
④ Used for cast steel parts, it can refine the as cast microstructure and improve cutting performance.
⑤ Used for large forgings, it can be used as the final heat treatment to avoid a greater tendency to crack during quenching.
⑥ Used for ductile iron to improve hardness, strength, and wear resistance, such as in the manufacture of important parts such as crankshafts and connecting rods for automobiles, tractors, and diesel engines.
⑦ Performing a normalization before the eutectic steel ball annealing can eliminate the mesh like secondary carbides and ensure that all carbides are spheroidized during the spheroidization annealing.
Last Words
The above is the main content summarized by the editor on how to understand Quenching, Tempering, Annealing, and Normalizing. Each heat treatment method requires precise control by heat treatment engineers. After reading this article, I believe everyone has a basic understanding of them. If you have any questions or inquiries about any heat treatment method, please contact our customer manager.