seamless vs erw pipe
- Share
- Issue Time
- Oct 9,2023
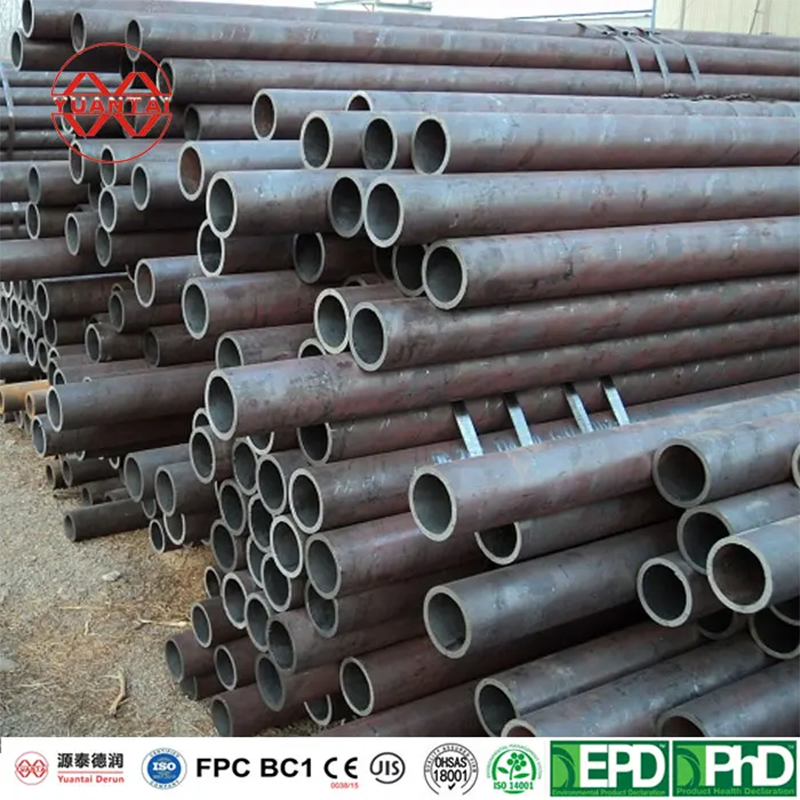
Manufacturing Process: Seamless pipes are formed by drawing a solid billet over a piercing rod to create a hollow tube, while ERW (Electric Resistance Welded) pipes are made by rolling a steel coil and welding the edges together under high pressure.
Strength and Durability: Seamless pipes are considered to be stronger and more durable compared to ERW pipes due to their uniform composition and absence of welded seams, which can be potential weak points.
Wall Thickness Consistency: Seamless pipes offer better wall thickness consistency throughout the length since they are milled or pierced to the desired thickness during the manufacturing process. ERW pipes, on the other hand, may have variations in wall thickness due to the welding process.
Cost Comparison: Seamless pipes are generally more expensive than ERW pipes due to the complex manufacturing process involved in their production. However, the cost difference may vary depending on the size and application requirements.
Availability and Customization Options: ERW pipes are readily available in various sizes and specifications, making them suitable for a wide range of applications. Seamless pipes, while not as readily available, can be custom-made to meet specific project requirements.
Application Suitability: Seamless pipes are often preferred in high-pressure and critical applications such as oil and gas pipelines, where the integrity of the pipe is paramount. ERW pipes find applications in less demanding environments, including water and sewage transportation.
Impact on Fluid Flow: The absence of weld seams in seamless pipes results in smooth internal surfaces, minimizing obstructions to fluid flow. On the other hand, the welded seams in ERW pipes may cause slight turbulence, affecting flow efficiency.
Welding Considerations: Seamless pipes eliminate the need for welding, reducing the risk of weld defects and associated quality issues. ERW pipes require welding, making them susceptible to potential weld-related problems.
Reliability and Longevity: Seamless pipes are known for their reliability and longevity, with fewer chances of failures due to their superior strength and consistent wall thickness. ERW pipes, although generally reliable, may be more prone to weld-related issues.
Consideration of Environmental Factors: Seamless pipes are better suited for applications in harsh environments, such as extreme temperatures or corrosive conditions, where their uniform composition provides enhanced resistance. ERW pipes may require additional protective coatings or materials in such situations.
Maintenance and Repairs: Seamless pipes typically require less maintenance and are less prone to leakages, reducing the need for frequent repairs compared to ERW pipes, which might require periodic inspections and maintenance due to the welded seams.
Impact on Project Timelines: The availability and lead time of seamless pipes can sometimes cause delays in project timelines, whereas ERW pipes are typically more readily available and have shorter lead times.
Quality Control and Inspection: The manufacturing process of seamless pipes allows for better control over quality and reduces the risk of defects. ERW pipes require consistent welding quality control and inspection to ensure integrity.
Standards and Regulations: Both seamless and ERW pipes are subjected to industry standards and regulations to ensure their safety and quality. However, seamless pipes may have stricter standards due to their critical applications.
Summary and Recommendation: In summary, both seamless and ERW pipes have their own advantages and considerations. Seamless pipes offer superior strength, durability, and consistency but come at a higher cost and may have longer lead times. ERW pipes are readily available, cost-effective, and suitable for less demanding applications. The choice between the two depends on the specific requirements and budget constraints of the project.