how to weld carbon steel pipe
- Share
- Issue Time
- Mar 26,2024
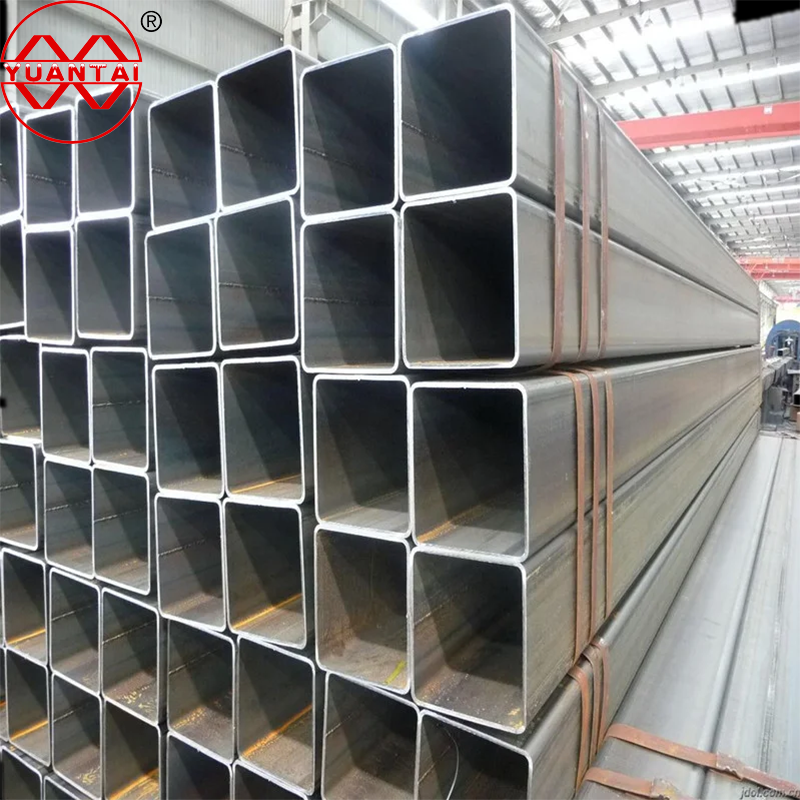
The most common method of connecting carbon steel pipes is through welded connections. These connections can be made using various methods, including electric welding, gas welding, and submerged arc welding. Manual arc welding and gas shielded welding are commonly used in electric welding.
Welded carbon steel pipes are made of carbon steel plates through welding processes, and can be customized in length and diameter as needed. Carbon steel pipes are available in a wide variety of specifications to meet the needs of various industries. Carbon steel pipes have good mechanical properties, high strength, good toughness, and wear resistance, so they are widely used in many industrial fields. For example, in the fields of petroleum, chemical industry, natural gas, etc., carbon steel pipes are used to transport liquids and gases.
Welding process of straight seam welded steel pipe: The use of small-size models can avoid stress corrosion, thermal cracking and deformation, and the electric welding current is 20% lower than that of high carbon steel. In order to ensure the arc ignition, DC reverse connection is adopted. The short arc welding strategy should slowly stop the arc, add arc pits, and finally weld and contact the surface of the material. In multi-layer high-rise electric welding, the temperature of the virtual beam should be controlled, and forced water cooling can be used after welding. There is no need to arc outside the slot; the wire joints should be connected correctly. The deformation after welding can only be corrected according to cold drawing.
Gas welding: Because gas welding is convenient and has strong matching ability, it can be used to weld a variety of indoor space parts. For some straight welded steel pipe components, such as thin plate structures, thin-walled pipes, etc., gas welding can sometimes be applied in the case of non-corrosion resistance. In order to avoid overheating, the ultrasonic mold is generally smaller than the high-carbon steel of the same thickness of electric welding. Gas cutting flame uses neutral flame, welding rod is selected according to the composition and characteristics of welding material, gas cutting powder uses gas flux 101, and electric welding uses left electric welding method. During welding, the slope of the top of the welding gun and the welding material should be 40°~50°, the flame core is about 2mm away from the molten pool, the top of the welding rod should contact the molten pool, move along the molten pool with the flame, the welding gun cannot shake horizontally, welding should be fast, and the interruption should be minimized.
Submerged arc welding: Submerged arc welding is suitable for medium-thin, left-right straight seam welded steel pipe plates. Submerged arc welding has high output rate and high cost-effectiveness of electric welding, but it is easy to cause segregation of aluminum alloy elements and residues.